Apollo Assist
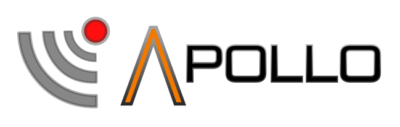
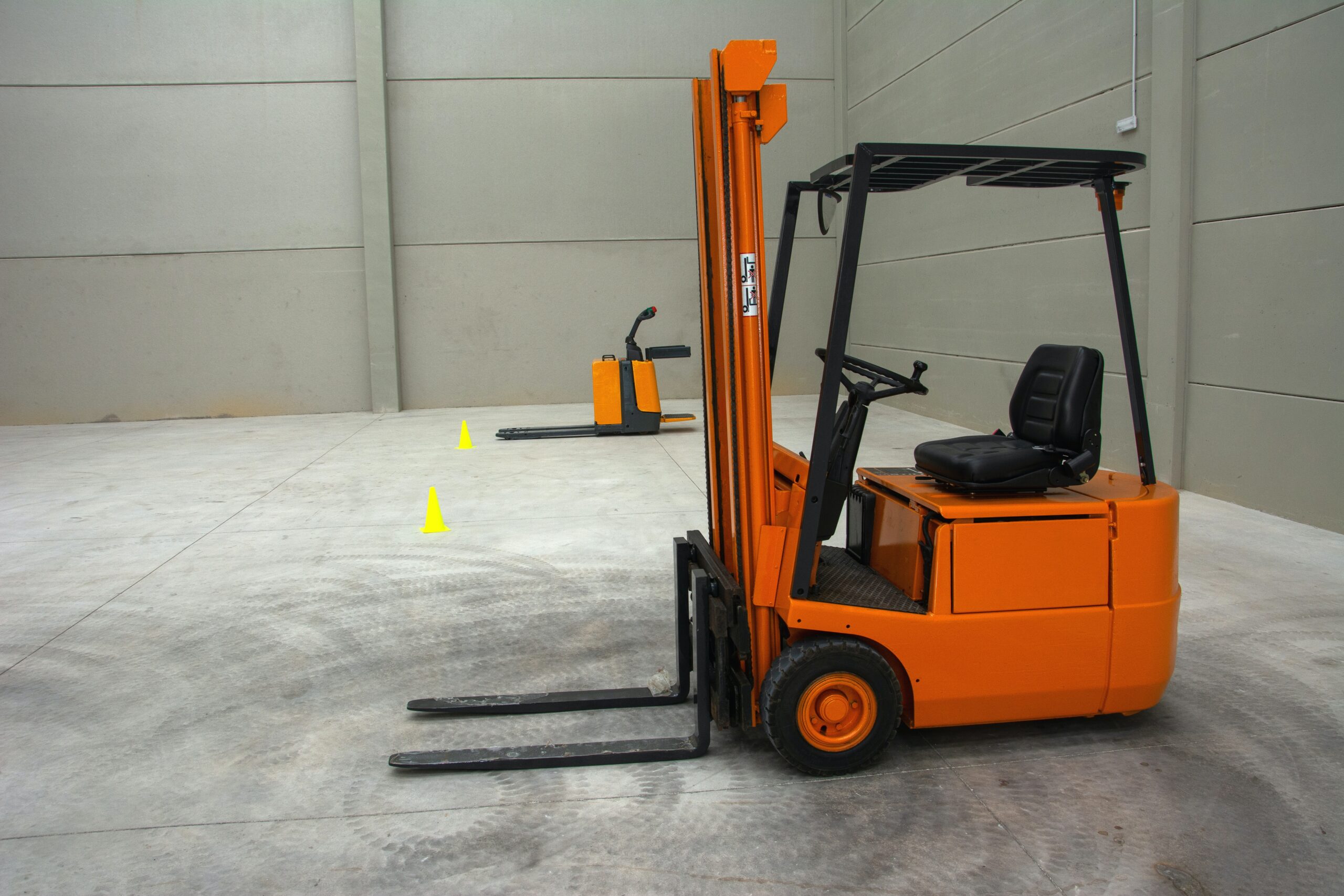
APOLLO ASSIST is an anti-collision system designed to support the forklift operator during operation. It is designed for use with the following types of vehicles: front forklift, reach truck, order picker. Main advantages of the system:
- Increase the level of occupational safety by detecting the part of the operator’s body that is outside the cab. If the operator extends his leg or arm outside the cab and the forklift is in motion, the sensor will indicate that the zone has been violated. This allows warning and remedial actions to be taken, such as activating sound signals, reducing the speed of the forklift or stopping it completely. The system is equipped with a speed reduction module and other forklift safety modules.
- Detection of a potential collision between a forklift that is moving backward and an obstacle nearby. An ultrasonic sensor will alert the operator and those in the immediate vicinity to the presence of an obstacle or object in front of the moving forklift. When such an event is detected, then the system will sound an audible signal, reduce the speed of the forklift or stop it completely to avoid a collision. This is a state-of-the-art safety support system.
- Reversing beacon – the system will activate an audible beacon to notify those around that the operator is performing a reversing maneuver.
Components of the Apollo Assist system
The Apollo Assist system consists of:
- Microprocessor controller. It is equipped with inputs/outputs for sensors and CAN interface (among other things, for reading the speed of the truck).
- CZ1 photoelectric sensor, which is mounted in the passage to the wheelchair cabin. It is responsible for detecting the operator’s limbs outside the cab. It is connected to the controller via a digital input.
- Ultrasonic sensor CZ2, which is mounted in the rear of the forklift. It is responsible for detecting obstacles.
- Beeper (sounder), which is connected to the controller via a digital output.
- Beacon, which is connected to the controller via a digital output.
- Speed reduction relay PR1, whose contacts allow reduction of the speed of the truck (when the CAN bus is not used for reduction).
- Travel stop relay PR2, whose contacts allow the cart to stop travel (when the CAN bus is not used for reduction).
- APOLLO ASSIST DIAG diagnostic application, which can be run on a smartphone or tablet. It allows you to connect wirelessly (Bluetooth) to the system. Through the application, it is possible to view current/active errors, alarms and warnings, as well as make changes to the device’s operating parameters. The customer can also monitor individual information from the vehicle’s CAN bus, as well as read, save or modify the system’s operating parameters.